i am optimistic about future ;of science helping people
1-
when
In short, an e-mailed spanner is just the start
Manufacturing's brave new future: 3D printing & the Internet of ...
BY USING THIS METHOD; THE FUTURE INTERNET ;INSTEAD OF 5 G MAY BE 1000 G OR MANY TIMES MORE
CAN SEND THROUGH INTERNET FOOD OR HEAVY ITEMS TO CUSTOMER ACROSS WORLD WITHOUT A CARRIER
Manufacturing’s brave new future: 3D printing & the Internet of Things
Once dismissed as a gimmick, 3D printing - or additive manufacturing - has finally come of age, according to Andy Gough, general manager at Datawright.
In December 2014, the crew of the orbiting International Space Station needed a ratcheting socket spanner. The only problem: there wasn’t one on board.
But the space station did have a 3D printer, shipped up on a re-supply flight the previous month. And so, using CAD instructions e-mailed to the space station by NASA, space station commander Barry Wilmore switched on the 3D printer and duly fabricated the required socket spanner.
Manufacturing mainstream
3D printing is rapidly finding its way out of the R&D laboratory, and into mainstream manufacturing. In short, producing real components for real products, sold to real customers.
For proof, look no further than the Paris Air Show last year, where Airbus proudly showed off its brand-new Airbus A350 XWB passenger jet, which contains more 3D printed components than any other aircraft currently flying – about 1,000 in all.
And aerospace, it turns out, is an ideal application for 3D-printed parts, offering a way to dramatically cut lengthy supply chains, while simultaneously producing parts that are cheaper and lighter than components that have been formed from traditional manufacturing processes.
The end of mass manufacturing
Fairly obviously, once an industry as demanding as aerospace makes the jump to a new technology, others will follow. That much is clear.
Events
Register for Additive 2016, taking place in Sheffield on Thursday 21 April, 2016 .
Register for Future of Making Things Roadshow – London,
Reports
Oracle and The Manufacturer have joined together to create The Manufacturer Industry 4.0 UK Readiness Report. Download the report for free now.
Read more manufacturing insights from Andy Gough here.
What’s less clear is how prepared businesses are for the revolution that will follow.
Consider the mass production model, unchanged since the Industrial Revolution of 250 years ago. At its simplest, it reduces the manufacture of every assembled product – however complex—to a series of steps.
Build a batch of component A, to start with. Then build a batch of component B. Then build a batch of component C, and so on. And then, when all the batches of components have been completed, begin assembly into a final finished product.
Changed manufacturing logic
And it has to be like that, because it’s inefficient and unproductive to make components one at a time. Until now, with 3D printing.
Few industries will escape this revolution, even our own, here at Datawright. Because enterprise applications such as MRP and ERP, don’t forget, have their roots in managing and coordinating the manufacture of those batches of components, choreographing their production, and bringing them all together at the right time for assembly.
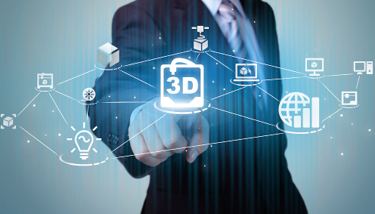
Don’t forget, either, that with 3D printing, some of the concepts underpinning all this, such as the economic batch quantity formula, have been quietly consigned to history.
The next manufacturing revolution
But as if all this weren’t enough, some manufacturing experts are pointing to the possibilities of combining 3D printing with another fast-emerging manufacturing revolution: the Internet of Things.
At first, no obvious connection seems plausible. 3D printing is—well—3D printing, and the Internet of Things is the connected world made possible by connecting Internet-enabled sensors to devices and objects.
In fact, there’s a very real connection between the two: the possibility of manufacturing objects that can uniquely declare what they are, and if necessary, broadcast that information.
Room temperature manufacturing
Now, with a component cut from a once-molten piece of metal, or extruded from an injection moulding machine, there is no opportunity to embed an RFID chip – the temperatures and pressures involved are far too high.
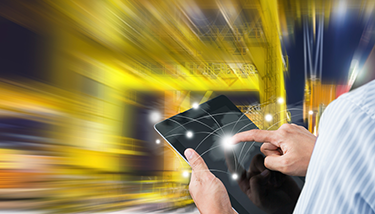
But with 3D printing, where objects are built up under room temperature conditions, at standard atmospheric pressure, adding an RFID chip is easily accomplished.
And once embedded, that RFID chip, unlike a detachable ‘tag’, is firmly and irrevocably part of the component. From a quality and product conformance point of view, it’s difficult to imagine a more secure way to maintain the ‘as built’ integrity of a product.
Advanced manufacturing in action
The implications are obvious, and yet, even so, some experts are pointing to a development with even greater potential, embedding unique three dimensional codes right inside the material of a 3D-printed object, capable of being read with the use of a terahertz scanner, a device that uses the part of the electromagnetic spectrum that lies between infrared and microwave light.
At a stroke, the shortcomings of RFID are overcome, because a 3D code can’t cease operating, or be jammed by electromagnetic interference.
Science fiction? Technologists at Carnegie Mellon University and Microsoft Research have already demonstrated such an approach in action.
The future is here
The moral of all this? An enormous revolution is underway, transforming the art of the possible, and manufacturers need to keep abreast of it.
In short, an e-mailed spanner is just the start.
......................................................
2- A WORLD WITHOUT THE SECOND OLDEST PROFESSIONa world without doctors
3- A WORLD WITHOUT THE OLDEST PROFESSIONa world without prostitutes
no:2 is already half way through according to my estimate- with remote surgery and on line consultation today.next will be remote surgery by AI and AI CONTROLLED ROBOT WITHOUT ANY HUMAN HELP IN DIAGNOSIS ANT TREATMENT
no:3 IS STILL IN ITS INFANCY BUT I CAN VISUALIZE HOW IT WILL BE IN FUTURE
FIRST:-
MINIATURISATION OF TOUCH MODULE;IN SURGICAL GLOVES NOW BEING USED BY SURGEONS IN REMOTE SURGERY
WHEN IT IS MICRO MINIATURIZED IT CAN BE USED TO LINE A CONDOM (INSTEAD OF A SURGICAL GLOVES AS IT IS TODAY FOR REMOTE SURGERY)
THIS ABOVE MENTIONED CONDOM IS WORN BY THE MALE PARTNER ;WHILE THE FEMALE PARTNER WILL HAVE A CORRESPONDING :-
Female Condom or Internal Condoms
WITH MICROMINIATURISED TOUCH MODULE LINED AS IN THE CONDOM
SECOND PART OF THIS INNOVATION WILL BE INTEGRATION OF THE PRESENT :-
Female Wireless Remote Control Vibrator/SEX TOY
SO WHAT THE MALE DOES THE FEMALE GETS AND VICE VERSA THROUGH INTERNET .IT WILL AN INTERNET COPULATION
THIS NEEDS MORE POWERFUL INTERNET MAY BE -INSTEAD OF 5 G MAY BE A MILLION GNEXT:-
WHAT I VISUALIZE IS
Holograms in Real Life: How the Technology Works and ...
Feb 3, 2021 5:51:15 AMcribe to our newsletterSign up to receive email updates on exclusive content and new product announcements.
m